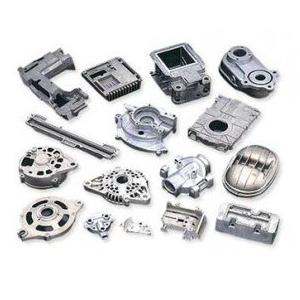
Add to Cart
Description
Custom Tungsten - Molybdenum Materiual For Formation And High- Temperature Processing Tool
TABLE 1 Composition, Density and Hardness Properties | |||
Class | Nominal Tungsten Weight % | Density g/cc | Hardness AB Rockwell "C" max |
1 | 90 | 16.85-17.25 | 32 |
2 | 92.5 | 17.15-17.85 | 33 |
3 | 95 | 17.75-18.35 | 34 |
4 | 97 | 18.25-18.85 | 35 |
A When specified by the purchaser, other hardness testing methods may be employed.
B For mechancially worked or aged material, the hardness can be as high as Rc46.
TABLE 2 Mechanical Properties, Minimum Values | |||||
Class | Ultimate Tensile Strength | Yield Strength at 0.2% Offset | Elongation,A% | ||
ksi | MPa | ksi | MPa | ||
1 | 110B | 758 | 75 | 517 | 5B |
2 | 110B | 758 | 75 | 517 | 5B |
3 | 105B | 724 | 75 | 517 | 5B |
4 | 100 | 689 | 75 | 517 | 2 |
A Determine with an extensometer accurate to 0.5% elongation or class.
B Nonmagnetic composition to Classes 1,2and 3 shall be 94 ksi(648 MPa) miinimum ultimate tensile strength . Minimum alongation shall be 2% on Classes 1 and 2 and 1% on Class 3.
1 Mold for Quartz Glass Stretched Pipe
Quartz glass can be applied to illumination technologies, semiconductor industry and optical fiber technologies. Besides the usage as crucibles and other materials in quartz glass continuous melting furnaces,
tungsten-molybdenum materials are necessary materials for manufacturing molds in the process of manufacturing large-sized high-precision quartz pipes.
2 Spinning Nozzles
Tungsten-molybdenum head pieces are feed opening of molten glass, which achieve a better liquid flow guidance effect and ensure the uniformity and stability of glass flow at the same time.
With higher high-temperature mechanical strength, difficult erosion from molten glass and difficult glass coloration, tungsten-molybdenum is a material for manufacturing.
3 Stirring Bar for Smelting
The stirring bar can eliminate glass bubbles when stirring glass solutions, to obtain molten glass with uniform temperature,
thus ensuring the quality and finished product rate of finished products.
Glass stirring bars are widely applied to the industries of optical glass, electronic glass, vessel glass and toy decoration glass.
With extremely strong high-temperature strength as well as difficult erosion from most of molten glass, tungsten-molybdenum materials are the optimal materials for manufacturing glass stirring bars.
4 Material for Die-casting Mold
In the process of die-casting iron/steel materials, the operating temperature of die-casting mold cavities can reach 1,000℃.
After severe oxidation, corrosion and scouring of cavity surfaces,
cavities will fail frequently because of severe plastic deformation and netty cracks, and can only die-cast dozens of or hundreds of parts.
Therefore, refractory alloys of tungsten, molybdenum, niobium and other alloys with the melting point of more than 2,600℃ can be used for manufacturing cavities of die-casting molds.
With the recrystallization temperature of more than 1,000℃, they can operate above this temperature for a long term.
Titanium-zirconium-molybdenum alloy represents molybdenum-based alloy while tungsten-molybdenum-nickle-iron represents tungsten-based alloy.
These kinds of materials feature extremely high melting point, better high-temperature strength, good heat resistance and corrosion resistance, excellent heat conductivity, thermal fatigue resistance,
no bonding with molten metal, good plasticity and convenient molding. It is mainly applied to die-casting molds of copper alloy and iron/steel materials operating at a higher temperature,
and can also be used as a thermal extrusion mold and other molds of titanium alloy and heat-resisting steel, with the service life far longer than that of other various kinds of hot work die steel.
With outstanding heat conductivity of tungsten-molybdenum-nickle-iron, it also takes advantages in large-batch continuous production of aluminum die castings in the automobile industry.
5 Hot Runner and Nozzle
The temperature of plastic melts can be accurately controlled in runner systems in the process of molding hot runner molds.
Plastics can flow into all the die cavities in a more uniform and consistent state, finally obtaining parts with consistent quality.
The part sprue for hot runner molding is high in quality, so hot runners can achieve low residual stress and small part deformation after
demolding. Therefore, many high-quality products on the market are produced by hot runner molds.
With extremely high heat conductivity, high-temperature strength, creep resistance, wear resistance and relatively strong corrosion resistance,
tungsten-molybdenum and its alloy materials are appropriate materials for manufacturing hot runner nozzles in injection molding machines and other kinds of injection molding equipment.
6 Molybdenum Piercing Mandrel
With excellent high-temperature strength and creep resistance, TZM alloy can be used for manufacturing mandril ejectors of seamless steel pipe penetration machines.
Molybdenum alloy ejectors are formed by adding rear earth materials into molybdenum powder raw materials through mixing, molding, appearance processing, high-temperature sintering and other processes,
with the finished product denstity of more than or equal to 9.4g/cm³. Molybdenum ejectors are mainly applied to perforation of seamless steel pipes made of stainless steel, drill steel, bearing steel, high-temperature alloy steel and so on.